Home
About Us
Split Power
Hole Design For DemoLetion
Benifits or Advantage
Technical Information
Contact Us
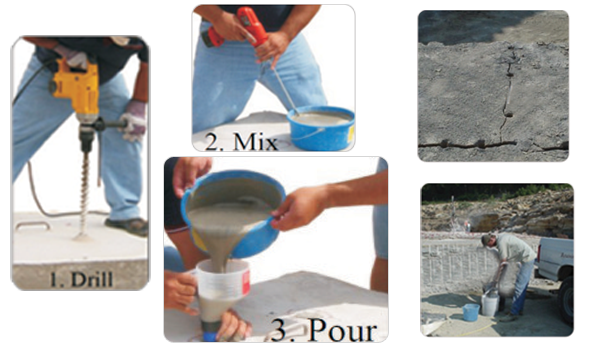
Best Practices to Use Split Power:
- Make sure you select the correct temperature specific to the weather.
- In order to obtain best results, it’s advisable to carry out experiment at first.
- When using SPLIT POWER with highly absorbent materials like concrete, the holes should be dampened before the mortar is poured, making sure however, that there is no presence of water.
- Large diameter holes positioned closer together accelerate breaking times.
- Make sure the holes are clean and no water and residues left in the holes, or use high-pressure air hose to clean out.
- Fresh mortar should be poured into holes within 5 minutes after mixing.
- Do not mix more than 2 bags ( 10 kg ) for each lot at a time.
- The feeding depth should be 100% of the pre-drilled holes.
- The workers need to take synchronized operation, especially to hard stone. The quantity of holes each worker responsible to fill has to be moderate. Taking synchronized steps when mixing, stirring and filling will lead to maximum expansive stress with all holes expand at the same time.
- Never use glass or metal containers for mixing.
- When mixing, if SPLIT POWER begins to steam in container, add some water to dilute and process properly.
- Cover holes to avoid direct sunlight. Example a tarp to provide shade or wet hay.
Safety and Material Handling:
Safety:
- Make sure that everyone working with split power understands the possibility of blowouts, and has read the technical instructions thoroughly.
- Split Power is a highly alkaline product, pH reaches 13 after contact with water and can cause severe irritation to mucous membranes, especially eyes. Skin and eye contacts with split power must be rinsed off with large amounts of cold water immediately without rubbing. Consult a doctor quickly.
- Wear safety goggles and rubber gloves during SPLIT POWER handling, mixing and filling. Dust-proof mask is recommended in poorly ventilated areas such as tunnels or mines.
- Plug the holes immediately after filling and cover the holes with straw mat. Keep your face away from the holes filled by mortar. Stay away from filled holes at least 3 hours after filling to avoid blow-out shot. Keep people away from job site after filling.
- Warm or bubbling mortar is forbidden to fill into holes. Once filled holes start to smoke or steam, that is the sign they may be about to blow out. Clear the area of people immediately.
- Keep people away from jobsite after filling holes. In case of people have to remain in the area, cover filled holes with a tarpaulin.
- Take care of fall of cracked block from the cracking object.
Split power finds its use in multiple industries such as Construction, Infrastructure, mining and all other industries where traditional explosives and dynamite is used for the purpose of breaking, cutting and demolishing.
Split power has many advantages over the traditional explosives:
1. Split Power is safe, easy to handle and use:
Since split power is based on the non-blowing expansive technology, it is very safe to handle with minimum training efforts. Also it is very safe to store and carry compared to the traditional explosives.
Ease of use: Split Power is very much easy to use as the user just have to mix it with water and add the mixture in the holes drilled into the rock or concrete. Since it is safer than traditional explosives, split power, no special licenses is needed to store it.
2. Pollution free:
Split Power is based on non-blowing expansive technology so:
a. It does not blows off sand, dust thereby not causing dust pollution
b. It does not cause sound pollution
c. The chemical used in split power causes no or very little pollution
3. Can be used for restricted demolition:
Split power finds its application extensively where restricted and controlled demolition is required. Such environments where restricted and controlled demolition is required may vary from underground tunneling, to controlled demolition of bridges, buildings etc.
4. Split- Power is silent cracking agent:
Unlike traditional explosives, split power is based on expansion caused by hydration technology which is recently evolved. Split Power thus does not make any noise, vibrations or does not cause explosion
5.Split- Power helps in planned, systematic and efficient demolition:
Since split power is based on expansive technology, the demolition can be very well controlled and carried out in systematic and planned manner. The demolition can be planned by drilling hole and pouring split power only where the demolition needs to be done.
Applications with respect to mining industry:
Production can be improved if Split power is used for mining operations, as there are no safety problems associated it
The dimensions of the block can be easily controlled if systematic demolition is carried out
Split power is alike traditional explosives so there are no debris and waste to clear on the worksite
Split power is ideal for the mining of jewel stones, as it does not affect the stones; it only cracks the surrounding stones.
Shelf life of Split power is One year -Two years depending on the storage conditions, i.e. humidity, ambient temperature etc. thus obviating problems associated with out-of-date material, as may be the case with explosives and detonator fuse.
Laborers and machines are safe as there is no explosion. Deeper and dangerous rocks can be mined using the split power due to its properties
Sr. No | Parameters | PVC Sleeves | INSULET SK-03 |
---|---|---|---|
1 | Form | Tubings | Free Flowing Liquid |
2 | Colour | RYB | All desired colour shades |
3 | Application | putting Tube on busbar andControlled heating for shrinkage | Simple spray techniquewith conventional spray tools. |
4 | Criticality of application | Skill operation a) chances of burning during heating process. b) chances of air bubble formationbetween sleeves & busbar.bubble formation. |
Non-skill operation & convenient process a) quick drying at room temperature. b) no chance of air bubble formation. |
5 | Surface of application | Not applicable on bendbusbars, twisted busbars and on the shapes other than straight.Not convenient for busbarshaving long length. | Geometry of busbars is notconstrained, can be applied on any shape &size of bushbars. |
6 | Puncture resistance | Poor. | Excellent. |
7 | In case of damage | Calls for complete replacement | Touch up possible at damaged areas. |
8 | In case of fire | Releases harmful chlorine gas. | Melts without any harmful releases. |
9 | Melts without any harmful releases. | Huge inventory as per sizes | Low Inventory. of busbar. |
10 | Dielectric strength | 2.5 KV | 80 micron 5 KV 1 mm 55 KV |
11 | Heat dissipation property | Satisfactory | Satisfactory |
12 | Thermal Stability | Stable up to 210º C | |
13 | Additional Features | Excellent Resistance to Chemicals & Corrosion/ Oxidation Re |